شمش فولادی یکی از محصولات اولیه صنعت فولاد است که از ذوب و قالبگیری سنگ آهن به دست میآید. این محصول به شکل بلوکهای بزرگ یا نوارهای ضخیم است و پایه بسیاری از محصولات فولادی دیگر به شمار میرود. از شمش فولادی در ساخت انواع مقاطع فولادی، لولهها، پروفیلها و دیگر محصولات استفاده میشود. در واقع، شمش فولادی ماده اولیهای است که به کمک فرآیندهای مختلف صنعتی، به اشکال و اندازههای گوناگون تبدیل میشود و در صنایع مختلف مانند خودروسازی، ساختمانسازی و تولید ماشینآلات کاربرد دارد.
معرفی شمش فولادی
شمش فولادی یکی از محصولات کلیدی و استراتژیک در زنجیره تولید فولاد محسوب میشود. این محصول بهعنوان ماده اولیه در
تولید انواع مقاطع فولادی، نقش پایهای و بنیادین دارد. شمش فولادی در واقع یک قالب جامد از فولاد مذاب است که پس از سرد
شدن، در اشکال مختلفی مانند بیلت (billet)، بلوم (bloom) یا اسلب (slab) تولید میشود.
در فرایند تولید،
فولاد پس از ذوب شدن در کورههای صنعتی، در قالبهایی با ابعاد مشخص ریخته میشود و پس از سرد شدن به شکل جامد درمیآید.
این فرآورده نیمهنهایی، از نظر ترکیب شیمیایی، استحکام، چگالی، و سایر خواص مکانیکی باید بهگونهای باشد که بتواند
پاسخگوی نیازهای فنی صنایع پاییندستی باشد.
شمش فولادی معمولاً دارای سطح مقطع مستطیلی یا مربعی است و ابعاد آن
متناسب با نوع کاربرد نهایی تنظیم میشود. یکی از مهمترین ویژگیهای شمش، یکنواختی در ساختار داخلی آن است که بر کیفیت
محصولات نهایی تأثیر مستقیم دارد.
کاربرد گسترده و اهمیت شمش فولادی در صنعت
شمش فولادی بهعنوان یکی از مهمترین مواد اولیه در صنایع فلزی، در گستره وسیعی از کاربردها مورد استفاده قرار میگیرد.
این محصول پایهگذار تولید انواع مقاطع فولادی مانند میلگرد، تیرآهن، نبشی، ناودانی، مفتول، لوله و ورق است.
صنایع
ساختمانی برای ساخت اسکلت فلزی، فونداسیون، ستونها و سقفها به میلگرد و تیرآهن نیاز دارند که همگی از شمش فولادی تولید
میشوند. در صنعت خودروسازی نیز بسیاری از قطعات شاسی، بدنه، سیستم تعلیق و انتقال نیرو از فولاد ساخته میشوند که منبع
اولیه آن، شمش فولادی است.
همچنین صنایع نفت، گاز و پتروشیمی، صنعت کشتیسازی، ساخت تجهیزات صنعتی، ابزارآلات سنگین،
پلسازی و حتی تولید لوازم خانگی، همگی به نوعی به شمش فولادی وابستهاند. بههمین دلیل، کیفیت شمشهای تولیدشده نهتنها
در عملکرد محصول نهایی تأثیر دارد، بلکه در کاهش هزینههای تولید، افزایش طول عمر سازهها و ایمنی آنها نیز نقش
تعیینکنندهای ایفا میکند.
در واقع، بدون شمش فولادی با کیفیت، ادامه زنجیره تأمین در صنایع فلزی ممکن نخواهد بود.
این اهمیت باعث شده که مجتمع فولاد ماهان، تمرکز ویژهای بر تولید شمش با استانداردهای بالا و کیفیت
یکنواخت داشته باشند.
انواع شمش فولادی
در صنعت فولاد، شمشها به عنوان محصولات نیمهنهایی شناخته میشوند که پایه و اساس تولید انواع مقاطع فولادی را تشکیل میدهند. بر اساس شکل و اندازه سطح مقطع، شمشهای فولادی معمولاً به سه گروه اصلی تقسیم میشوند: بیلت (Billet)، بلوم (Bloom) و اسلب (Slab) یا تختال. هر یک از این انواع، دارای مشخصات فنی و کاربردهای متفاوتی در زنجیره تولید فولاد هستند. شناخت این تفاوتها به تولیدکنندگان، صنعتگران و حتی خریداران کمک میکند تا محصول مناسب نیاز خود را انتخاب کنند.
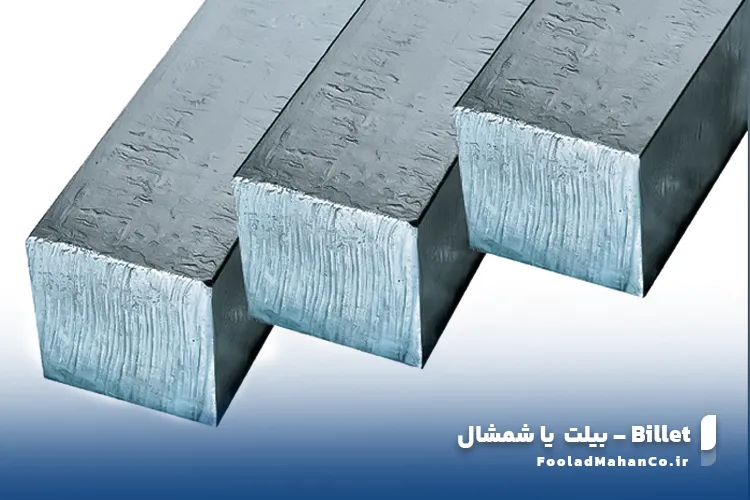
شمش بیلت (Billet) یا شمشال
بیلت یکی از رایجترین انواع شمش فولادی است که سطح مقطع آن به صورت مربعی یا گاهی دایرهای بوده و ابعاد آن معمولاً در محدودهی ۱۰۰×۱۰۰، ۱۲۰×۱۲۰، ۱۲۵×۱۲۵، ۱۳۰×۱۳۰ و حداکثر ۱۵۰×۱۵۰ میلیمتر قرار دارد. در بازار فولاد، اگر شمش مستقیماً از فرآیند ریختهگری مداوم (CCM) وارد نورد شود، به آن شمش ccm یا بیلت گفته میشود.
کاربردهای بیلت:
- تولید میلگردهای ساختمانی و صنعتی
- ساخت سیم مفتول
- تولید انواع نبشی، ناودانی و پروفیلهای سبک
- ساخت قطعات دقیق در صنعت خودروسازی یا ماشینسازی
بیلتها به دلیل اندازه کوچکتر، قابلیت شکلپذیری بالا و یکنواختی در ترکیب شیمیایی، در خطوط نورد پیوسته کاربرد فراوانی دارند و یکی از اصلیترین محصولات مجتمع فولاد ماهان محسوب میشوند.
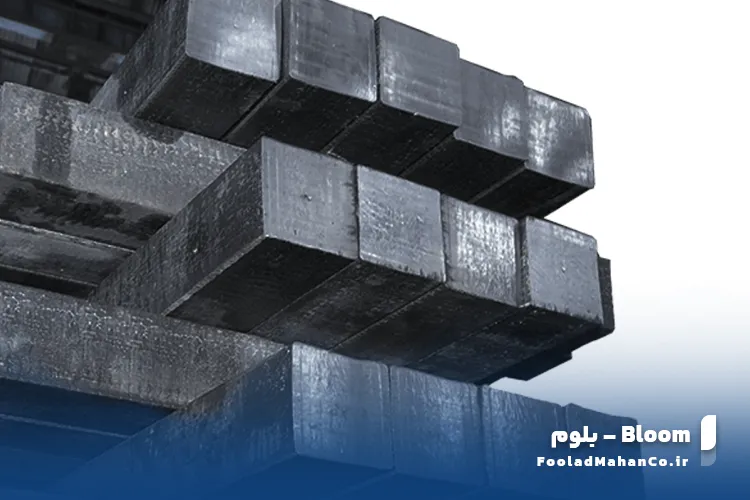
شمش بلوم (Bloom)
بلوم نوعی دیگر از شمش فولادی است که از نظر ظاهر بسیار شبیه به بیلت است، اما ابعاد بزرگتری دارد. سطح مقطع بلوم
معمولاً مربعی و در اندازههای ۱۸۰×۱۸۰، ۲۰۰×۲۰۰ یا حتی ۲۵۰×۲۵۰ میلیمتر تولید میشود.
در گذشته، شمشهایی با
سایزهای بالا را بلوم مینامیدند، اما امروزه در بسیاری از واحدهای فولادی به این نوع محصول، به ویژه اگر مستقیماً در
نورد استفاده شود، شمش فابریک نیز گفته میشود. هرچند که فرآیند تولید بیلت و بلوم یکسان است، اما تفاوت آنها در سایز و
کاربرد است.
کاربردهای بلوم:
- تولید تیرآهن سنگین و مقاطع H یا I
- ساخت ریل راهآهن
- تولید میلگردهای صنعتی با قطر بالا
- ساخت ناودانی و نبشی سنگین
- تولید محور و شاسی تجهیزات صنعتی
بلومها بهدلیل ابعاد بزرگتر، معمولاً برای مقاطع صنعتی سنگین و پروژههای عمرانی، سدسازی و پلسازی کاربرد دارند که نیازمند استحکام بالا و ابعاد بزرگتر هستند.
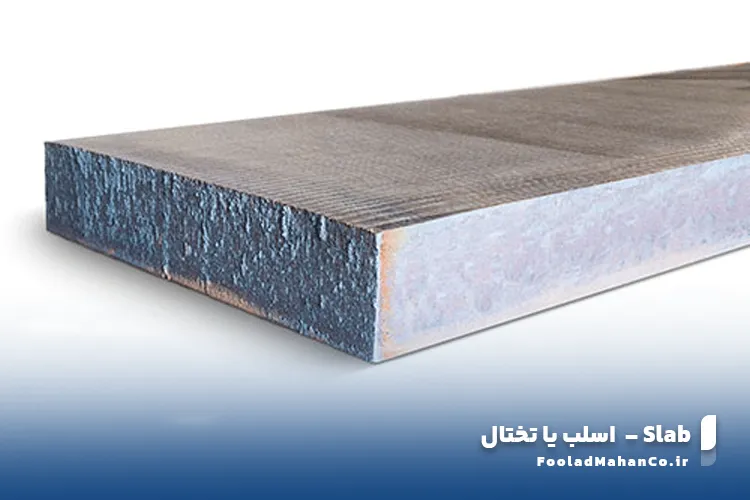
اسلب (Slab) یا تختال
اسلب که در فارسی گاهی با نام تختال شناخته میشود، نوعی شمش فولادی با سطح مقطع مستطیلی شکل است که ابعاد رایج آن در ایران معمولاً ۱۲۰۰×۲۰۰ یا ۱۲۰۰×۲۵۰ میلیمتر است و به طولهایی تا ۱۲۰۰۰ میلیمتر تولید میشود. اسلب برخلاف بیلت و بلوم که مقاطع طویل تولید میکنند، ماده اولیه برای ساخت محصولات پهن فولادی است.
کاربردهای اسلب:
- تولید ورقهای فولادی گرم و سرد
- ورقهای گالوانیزه، آجدار و رنگی
- لولههای فولادی درزدار و بدون درز
- پروفیلهای صنعتی و ساختمانی
- صنایع خودروسازی، مخزنسازی و کشتیسازی
شرکتهایی مانند فولاد خوزستان در حال حاضر تولیدکننده اصلی اسلب در ایران هستند. همچنین با اجرای پروژههایی مانند توسعه فولاد اکسین، در آینده شاهد تولید اسلبهایی با عرض بسیار بیشتر (تا ۴۵۰۰ میلیمتر) خواهیم بود که نیاز صنایع خاص مانند کشتیسازی و سازههای عظیم صنعتی را تأمین خواهد کرد.
جمعبندی: تفاوت انواع شمش در یک نگاه
نوع شمش | شکل مقطع | ابعاد رایج (mm) | کاربرد اصلی |
بیلت (Billet) | مربع یا دایره | 100×100 تا 150×150 | میلگرد، مفتول، نبشی سبک |
بلوم (Bloom) | مربع بزرگتر | 180×180 تا 250×250 | تیرآهن، ریل، مقاطع صنعتی |
اسلب (Slab) | مستطیل | 1200×200 یا 250×12000 | ورق فولادی، لوله، پروفیل |
فرآیند تولید شمش فولادی
تولید شمش فولادی یکی از مراحل کلیدی در زنجیره تولید فولاد به شمار میرود و نقش پایهای در تأمین مواد اولیه بسیاری از
محصولات فولادی دارد. این فرآیند شامل مجموعهای از عملیات حرارتی و مکانیکی است که طی آن، مواد اولیه حاوی آهن به فولاد
مذاب تبدیل شده و در نهایت به شکل شمش منجمد میشوند.
برای تولید شمش فولاد، از روشهای مختلفی استفاده میشود. در
میان این روشها، کوره القایی و کوره قوس الکتریکی دو شیوه رایج در صنعت فولاد هستند. هر یک از این روشها ویژگیها و
مزایای خاص خود را دارند و در انتخاب آنها عوامل متعددی از جمله ظرفیت تولید، کیفیت مورد انتظار و هزینههای عملیاتی
نقش دارند.
مواد اولیهای که در این فرآیند استفاده میشوند، معمولاً شامل سنگ آهن، آهن اسفنجی، و قراضههای فولادی
هستند. این مواد پس از آمادهسازی، وارد کورههای ذوب شده و در دمای بالا به فولاد مذاب تبدیل میشوند. سپس این مذاب تحت
شرایط کنترلشده به واحد ریختهگری منتقل شده و به شکل شمش در قالبهای مخصوص شکل میگیرد.
مجتمع فولاد ماهان نیز از
روش کوره القایی و ریختهگری مداوم (CCM) برای تولید شمش فولادی بهره میبرد. این شیوه، ضمن برخورداری از دقت بالا و
انعطافپذیری در تولید، امکان تولید شمشهایی با کیفیت مطلوب و در ابعاد متنوع را فراهم میسازد.
پس از قالبگیری و
خنکسازی، شمشهای تولیدی آماده برش، انبارش یا ارسال به واحدهای نورد و تولید مقاطع فولادی میشوند. این شمشها بسته به
نوع روش تولید، میتوانند در کیفیت نهایی، خواص مکانیکی، و ترکیب شیمیایی با یکدیگر تفاوتهایی داشته باشند.
در
مجموع، فرآیند تولید شمش فولادی با وجود پیچیدگیهای فنی، ساختاری منطقی و هدفمند دارد که در آن تبدیل مواد اولیه به یک
محصول قابل استفاده صنعتی با دقت و کنترل بالا صورت میگیرد. استفاده از فناوریهای نوین و بهروز، نقش مهمی در بهبود
کیفیت و افزایش بهرهوری این فرآیند ایفا میکند.
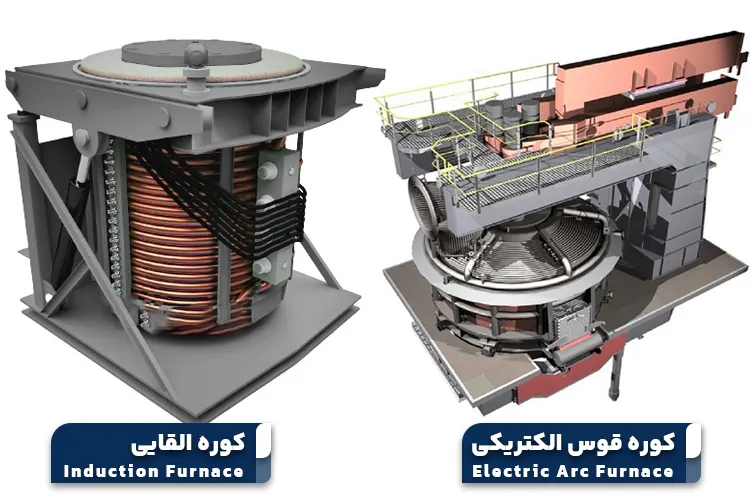
تفاوت شمش تولیدشده با کوره قوس و کوره القایی
هرچند هر دو روش قوس الکتریکی و القایی با هدف تولید فولاد مذاب به کار گرفته میشوند، اما تفاوتهای اساسی در عملکرد،
کیفیت محصول نهایی و توان تصفیه مواد دارند که موجب تمایز میان شمشهای تولیدی در این دو فرایند میشود.
در روش کوره
قوس الکتریکی، امکان اعمال دقیقتر کنترل بر روی ترکیب شیمیایی فولاد فراهم است. این کورهها مجهز به سیستمهای تصفیه
مذاب هستند که اجازه میدهد ناخالصیهایی مانند گوگرد و فسفر تا حد زیادی حذف شوند. نتیجه این فرآیند، فولادی با ترکیب
یکنواخت، عناصر مضر کمتر و امکان تولید شمشهایی با کربن پایین و کیفیت بالا است. به همین دلیل شمشهای تولیدشده با این
روش معمولاً از نظر آنالیز شیمیایی، یکنواختتر بوده و استانداردهای کیفی بالاتری را کسب میکنند.
در مقابل، کورههای
القایی اگرچه از نظر راهاندازی سادهتر و کمهزینهتر هستند، اما محدودیتهایی در فرآیند تصفیه دارند. یکی از چالشهای
اصلی این روش، کنترل ضعیف اکسیژن محلول در مذاب است. این موضوع میتواند منجر به اکسید شدن فروآلیاژها و کاهش کیفیت
نهایی شمش شود. همچنین عملیات فسفرزدایی و گوگردزدایی در کوره القایی با دشواری بیشتری انجام میپذیرد، چراکه این دو
فرآیند در شرایط دمایی متفاوتی مؤثر واقع میشوند و جمع آنها در یک فرایند، کنترل ترکیب شیمیایی را سختتر
میکند.
اگرچه میتوان با افزودن تجهیزات جانبی مانند کوره پاتیلی LF یا LRF بسیاری از این ضعفها را پوشش داد، اما
به دلیل هزینههای بالای انرژی، مواد مصرفی و نگهداری، این تجهیزات در اکثر واحدهای فولادسازی با کوره القایی در کشور
مورد استفاده قرار نمیگیرند. در کنار این چالشها، باید به قدمت ماشینآلات ریختهگری نیز اشاره کرد. بسیاری از خطوط
ریختهگری مداوم در کشور، ساخت داخل یا وارداتی از کشورهایی مانند چین و هند هستند که معمولاً تکنولوژی آنها قدیمی و
فاقد سیستمهای دقیق کنترلی است.
در نتیجه، میتوان گفت که:
- شمشهای تولیدشده با کوره قوس الکتریکی از دقت آنالیز بالاتر، یکنواختی بیشتر، و کیفیت شیمیایی مطلوبتری برخوردارند.
- شمشهای حاصل از کوره القایی اگرچه هزینه تولید کمتری دارند، اما در نبود سیستم تصفیه و با توجه به محدودیتهای ماشینآلات، معمولاً دارای نوسانات بیشتری در ترکیب شیمیایی و کیفیت نهایی هستند.
با این حال، چنانچه واحدی از تجهیزات تصفیه مناسب و ماشینآلات بهروز استفاده کند، شمش تولیدی با کوره القایی نیز میتواند با کیفیت بسیار خوبی تولید شود.
تفاوت آنالیز شمشهای فولادی 3SP و 5SP
شمشهای فولادی یکی از پایههای اصلی صنایع فولاد هستند که در گریدهای مختلفی تولید میشوند. دو گرید رایج و کاربردی این محصولات، 3SP و 5SP هستند که براساس استاندارد روسی GOST 380 تعریف شدهاند. هر یک از این گریدها ویژگیهای مکانیکی خاصی دارند و در کاربردهای متفاوتی مورد استفاده قرار میگیرند.
مجتمع فولاد ماهان با بهرهگیری از تجهیزات بهروز و کنترل دقیق کیفیت، توانسته است شمشهای فولادی با آنالیزهای 3SP و 5SP را با بالاترین استانداردهای صنعتی تولید و روانه بازار کند. این مجموعه با نظارت دقیق بر ترکیب شیمیایی و خواص مکانیکی محصولات خود، نیاز صنایع پاییندستی را با کیفیتی پایدار و قابل اطمینان تأمین میکند.
شمش فولادی 3SP
شمشهای 3SP به دلیل انعطافپذیری بیشتر و مقدار کربن پایینتر، گزینهای ایدهآل برای قطعاتی هستند که نیاز به فرمدهی و جوشکاری بالا دارند. معمولاً این گرید برای تولید:
- نبشی و ناودانی،
- میلگردهای سایز ریز
- و سایر مقاطع سبک فولادی
استفاده میشود. درصد پایینتر عناصر آلیاژی، شکلپذیری بیشتری را به این نوع شمش میبخشد و همین موضوع، آن را به محصولی با قیمت بالاتر و کیفیت فنی برتر تبدیل میکند.
شمش فولادی 5SP
در مقابل، شمشهای 5SP دارای استحکام بالاتر و مقدار کربن بیشتر هستند که این ویژگی باعث کاهش انعطافپذیری ولی افزایش مقاومت مکانیکی محصول نهایی میشود. این گرید اغلب برای:
- میلگردهای سایز 12 تا 25 میلیمتر،
- کلافهای صنعتی
مورد استفاده قرار میگیرد. همچنین در ساخت میلگردهای سنگینتر، از گریدهایی با استحکام بالاتر بهره گرفته میشود.
مزایای استفاده از شمش فولادی با کیفیت بالا
استفاده از شمش فولادی با کیفیت بالا، یکی از مهمترین عوامل در تضمین کیفیت و صرفهجویی در فرآیندهای تولیدی صنایع فولاد و ساختوساز بهشمار میرود. انتخاب دقیق مواد اولیه، تأثیر مستقیمی بر عملکرد خط تولید، طول عمر تجهیزات و کیفیت محصول نهایی خواهد داشت. در ادامه به مزایای کلیدی استفاده از شمشهای مرغوب میپردازیم:
کاهش ضایعات در فرآیند تولید
شمشهای با کیفیت بالا دارای ترکیب شیمیایی یکنواخت، عاری از
ناخالصیهای مزاحم مانند گوگرد و فسفر، و بدون عیوب ساختاری هستند. این ویژگیها باعث میشوند فرآیند نورد یا ذوب ثانویه
با دقت و ثبات بیشتری انجام شود و میزان ضایعات ناشی از شکست، تاببرداشتن یا ترکخوردگی بهطور چشمگیری کاهش یابد.
تولید محصول نهایی با کیفیتتر
شمش مرغوب پایهگذار تولید میلگرد، تیرآهن، نبشی و دیگر مقاطع فولادی
با سطح کیفی بالا است. یکنواختی در آنالیز شیمیایی و خواص مکانیکی، موجب تولید محصولی میشود که:
- استانداردهای ملی و بینالمللی را پوشش میدهد،
- استحکام، انعطاف و دوام قابل اطمینانتری دارد،
- و برای مصرفکننده نهایی ارزش بالاتری ایجاد میکند.
افزایش بهرهوری در خط تولید
استفاده از شمش استاندارد و با کیفیت، باعث پایداری در عملیات نورد و
جلوگیری از توقفهای ناخواسته در خط تولید میشود. این موضوع باعث:
- کاهش زمان تنظیم دستگاهها،
- کاهش نیاز به تعمیرات ناشی از ناهنجاریهای متالورژیکی،
- و در نهایت افزایش سرعت تولید و کاهش هزینههای سربار خواهد شد.
مجتمع فولاد ماهان؛ تضمین کیفیت از ابتدا تا انتها
مجتمع فولاد ماهان با تمرکز بر تولید شمش فولادی
در آنالیزهای دقیق و با بهرهگیری از تجهیزات مدرن کوره القایی و ماشین ریختهگری مداوم (CCM)، شرایط لازم برای تولید
شمشهای با کیفیت و پایدار را فراهم کرده است. شمشهای تولیدی این مجموعه، نه تنها در کاهش ضایعات و افزایش کیفیت
مؤثرند، بلکه بهرهوری کل زنجیره تأمین را نیز بهبود میبخشند.
جمعبندی و نکات پایانی
در دنیای امروز که صنایع فولادی با سرعت در حال پیشرفت و رقابت هستند، انتخاب شمش فولادی مناسب و با کیفیت بالا نقش کلیدی
در موفقیت خطوط تولید و کاهش هزینهها ایفا میکند. شمش بهعنوان ماده اولیه اصلی در تولید محصولات نهایی همچون میلگرد،
نبشی، ناودانی و سایر مقاطع فولادی، اگر از کیفیت مطلوبی برخوردار نباشد، میتواند مشکلات متعددی از جمله ترکهای سطحی،
ناپایداری در آنالیز شیمیایی، و کاهش استحکام مکانیکی را به همراه داشته باشد.
از سوی دیگر، استفاده از شمشهای با
آنالیز دقیق، همگن و عاری از ناخالصیهای مضر، باعث میشود فرآیند نورد روانتر انجام شده، دستگاهها با حداقل توقف کار
کنند و میزان ضایعات کاهش یابد. نتیجه نهایی، افزایش کیفیت محصول نهایی، صرفهجویی در هزینههای تولید، و ارتقای
بهرهوری کل کارخانه خواهد بود. این موضوع بهویژه برای واحدهای تولیدی که به دنبال ثبات در کیفیت و توسعه بازار خود
هستند، بسیار حیاتی است.
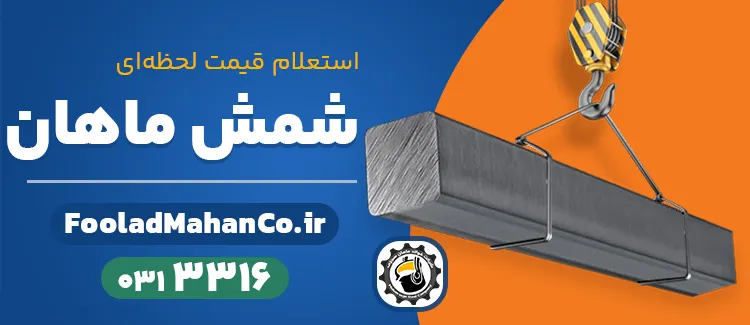
مجتمع فولاد ماهان با بهرهگیری از فناوری روز دنیا، کورههای القایی مدرن و ماشین
ریختهگری مداوم (CCM)، توانسته است شمشهایی با گریدهای 3SP و 5SP تولید کند که پاسخگوی نیاز صنایع ساختمانی،
نورد، و میلگردسازی است. شمشهای این مجموعه با کنترل دقیق کیفی و آنالیز شیمیایی استاندارد، گزینهای مطمئن برای
مشتریان حرفهای محسوب میشوند.
برای اطلاع از قیمت روز شمش فولادی، میتوانید به بخش قیمت شمش فولادی در سایت مراجعه
کرده و بهصورت لحظهای استعلام قیمت دریافت نمایید. همچنین، در صورت نیاز به مشاوره یا خرید، کارشناسان فروش
مجتمع فولاد ماهان آماده پاسخگویی و راهنمایی شما هستند.